︎︎︎ Conscious Design ︎︎︎ Articles
Interdisciplinary experience and the path to environmentally responsible material: Interview with the founder of Malai
Interdisciplinary experience and the path to environmentally responsible material: Interview with the founder of Malai
9. 11. 2023 Interdisciplinary Collaboration
Zuzana Gombošová
Zuzana Gombošová
Zuzana Gombošová MA
Founder of Malai Biomaterials, a company based in India that focuses on the development of composite materials (combination of hemp fibres and bacterial cellulose) with properties and appearance similar to leather. She studied textile design in Liberec, Czechia and Istanbul, Turkey. She completed the Master's course 'Textile Futures (Material Futures)' – University of the Arts London – Central Saint Martins. Zuzana is dedicated to materials research, design of new materials and their further development in cooperation with experts from other fields.
Founder of Malai Biomaterials, a company based in India that focuses on the development of composite materials (combination of hemp fibres and bacterial cellulose) with properties and appearance similar to leather. She studied textile design in Liberec, Czechia and Istanbul, Turkey. She completed the Master's course 'Textile Futures (Material Futures)' – University of the Arts London – Central Saint Martins. Zuzana is dedicated to materials research, design of new materials and their further development in cooperation with experts from other fields.

1
An interview about how Zuzana perceives the role of an environmentally conscious designer and about her perspective on interdisciplinary collaboration. The founder of 'Malai Biomaterials' shares how her experience in the Turkish fashion industry led her to studying the 'Textile Futures (Material Futures)' course. She describes the beginnings of working with bacterial cellulose and the experience of approaching scientific specialists. In the interview, you will learn how the company was founded, how it operates and how interdisciplinary cooperation continues today.
Can you please introduce your specialisation and what you're currently working on?
Zuzana: I have a rather broad focus at the moment. My background is in textile and clothing design. I later studied for a master's degree, which is now called 'Material Futures'. The study was mainly focused on a design approach that uses research methodologies and borrows methodologies from other disciplines such as science, architecture and various other disciplines. That's where I started to focus on working with bacterial cellulose, which was also the subject of my final project.
Since then, I've been engaged in material research and at the same time designing new materials and further developing them in cooperation with experts from other fields.
Since 2017/2018, I've been leading the 'Malai' start-up operating in Slovakia and India. It focuses on the development of biocomposite materials based on bacterial cellulose, which is grown on agricultural waste.
Do you also work on other kinds of materials under the 'Malai' brand?
Sometimes. There isn't always enough time and professional capacity to work with completely different material. It happens, however, that companies contact us about their waste material, which they would like to use. Sometimes I also collaborate with other projects, e.g. with Vlasta from 'Crafting plastics!'. And even before that I collaborated with an Indian company with a very broad production focus – I worked with their entire portfolio of waste materials. Since then, I've mainly been dealing with biomaterials/materials with bacterial cellulose.
You mentioned that before you followed up your master's project by founding 'Malai', you worked in an Indian company?
Yes, about a year after graduating, I devoted myself to the project and presented it, but the creation of 'Malai' was essentially a coincidence. I came to India because of another job, which gradually led me to coconuts and bacterial cellulose grown on their waste. However, this technology wasn't developed there, so we started working on it with the knowledge from my study.
How was 'Malai' founded and in cooperation with whom?
It was founded by me and my former colleague and partner Susmith CS, a designer and mechanical engineer.
Is this an ongoing cooperation?
Susmith is now only involved externally, he's working on other projects. We worked together for 3 years.
What motivated you to start this project? Untapped potential of the source material?
The potential was definitely there, but in 2017, bacterial cellulose wasn't a well-known term at all, so we had a lot of explaining to do. As far as motivation is concerned, I've been dealing with sustainability for a long time before. And in that large Indian company, I realised that the use of waste materials in their quantities wouldn't be a sufficient solution. During the processing of these materials and their return to circulation, additional, new problems arise. That's why I decided to focus on materials that will be naturally degradable and the end of their useful life will not be a problem. I think Susmith had similar motivations, except that coconut production was part of his culture and an interesting topic for him.
How (if at all) have the above mentioned motivations and goals changed over time?
Starting a business and building our own company was new for both of us, so the original motivation was sometimes lost among new responsibilities and problems. However, it's necessary to stick to your initial vision in order to overcome these difficult parts. That said, it isn't necessary to stick to your ideals completely, you must be flexible as long as your basic values allow it. When building 'Malai', we emphasised that there would be no synthetic, non-degradable admixture in the material. We focused mainly on developing a material whose production will work with the environment where it is produced and with its origin. We actually built the company around an already functioning biotope, so that it doesn't disturb the value system not only for the end customer, but also for the people who create it and the system that provides the material for its operation. It's challenging and you need the right people at the right time. The initial inspiration and goals remained, of course new ones were added over time, while we were learning.
I'd like to find out more about the functioning of the company in practice. For example, I'd like to know how big the company is?
Our team consists of approximately ten people. Of course, we work with external consultants and experts.
What are the specialisations of your colleagues on the team? Are there designers, scientists and engineers among them?
We don't have scientists, although we could use them. We mainly work with them externally, as they need laboratories and workplaces, which we currently don't have. Therefore, we cooperate with scientific and technical institutes, which, in addition to experts, also provide us with laboratories and testing equipment.
In that narrow team, we have people directly from the production's location. They are personally trained and are in charge of various aspects of production. Then there are salespeople who deal with sales and marketing, and there's one designer and one mechanical engineer. I hold many different roles. The scientists we work with are microbiologists, material scientists, experts in polymer science, and mostly chemists.
Zuzana: I have a rather broad focus at the moment. My background is in textile and clothing design. I later studied for a master's degree, which is now called 'Material Futures'. The study was mainly focused on a design approach that uses research methodologies and borrows methodologies from other disciplines such as science, architecture and various other disciplines. That's where I started to focus on working with bacterial cellulose, which was also the subject of my final project.
Since then, I've been engaged in material research and at the same time designing new materials and further developing them in cooperation with experts from other fields.
Since 2017/2018, I've been leading the 'Malai' start-up operating in Slovakia and India. It focuses on the development of biocomposite materials based on bacterial cellulose, which is grown on agricultural waste.
Do you also work on other kinds of materials under the 'Malai' brand?
Sometimes. There isn't always enough time and professional capacity to work with completely different material. It happens, however, that companies contact us about their waste material, which they would like to use. Sometimes I also collaborate with other projects, e.g. with Vlasta from 'Crafting plastics!'. And even before that I collaborated with an Indian company with a very broad production focus – I worked with their entire portfolio of waste materials. Since then, I've mainly been dealing with biomaterials/materials with bacterial cellulose.
You mentioned that before you followed up your master's project by founding 'Malai', you worked in an Indian company?
Yes, about a year after graduating, I devoted myself to the project and presented it, but the creation of 'Malai' was essentially a coincidence. I came to India because of another job, which gradually led me to coconuts and bacterial cellulose grown on their waste. However, this technology wasn't developed there, so we started working on it with the knowledge from my study.
How was 'Malai' founded and in cooperation with whom?
It was founded by me and my former colleague and partner Susmith CS, a designer and mechanical engineer.
Is this an ongoing cooperation?
Susmith is now only involved externally, he's working on other projects. We worked together for 3 years.
What motivated you to start this project? Untapped potential of the source material?
The potential was definitely there, but in 2017, bacterial cellulose wasn't a well-known term at all, so we had a lot of explaining to do. As far as motivation is concerned, I've been dealing with sustainability for a long time before. And in that large Indian company, I realised that the use of waste materials in their quantities wouldn't be a sufficient solution. During the processing of these materials and their return to circulation, additional, new problems arise. That's why I decided to focus on materials that will be naturally degradable and the end of their useful life will not be a problem. I think Susmith had similar motivations, except that coconut production was part of his culture and an interesting topic for him.
How (if at all) have the above mentioned motivations and goals changed over time?
Starting a business and building our own company was new for both of us, so the original motivation was sometimes lost among new responsibilities and problems. However, it's necessary to stick to your initial vision in order to overcome these difficult parts. That said, it isn't necessary to stick to your ideals completely, you must be flexible as long as your basic values allow it. When building 'Malai', we emphasised that there would be no synthetic, non-degradable admixture in the material. We focused mainly on developing a material whose production will work with the environment where it is produced and with its origin. We actually built the company around an already functioning biotope, so that it doesn't disturb the value system not only for the end customer, but also for the people who create it and the system that provides the material for its operation. It's challenging and you need the right people at the right time. The initial inspiration and goals remained, of course new ones were added over time, while we were learning.
I'd like to find out more about the functioning of the company in practice. For example, I'd like to know how big the company is?
Our team consists of approximately ten people. Of course, we work with external consultants and experts.
What are the specialisations of your colleagues on the team? Are there designers, scientists and engineers among them?
We don't have scientists, although we could use them. We mainly work with them externally, as they need laboratories and workplaces, which we currently don't have. Therefore, we cooperate with scientific and technical institutes, which, in addition to experts, also provide us with laboratories and testing equipment.
In that narrow team, we have people directly from the production's location. They are personally trained and are in charge of various aspects of production. Then there are salespeople who deal with sales and marketing, and there's one designer and one mechanical engineer. I hold many different roles. The scientists we work with are microbiologists, material scientists, experts in polymer science, and mostly chemists.
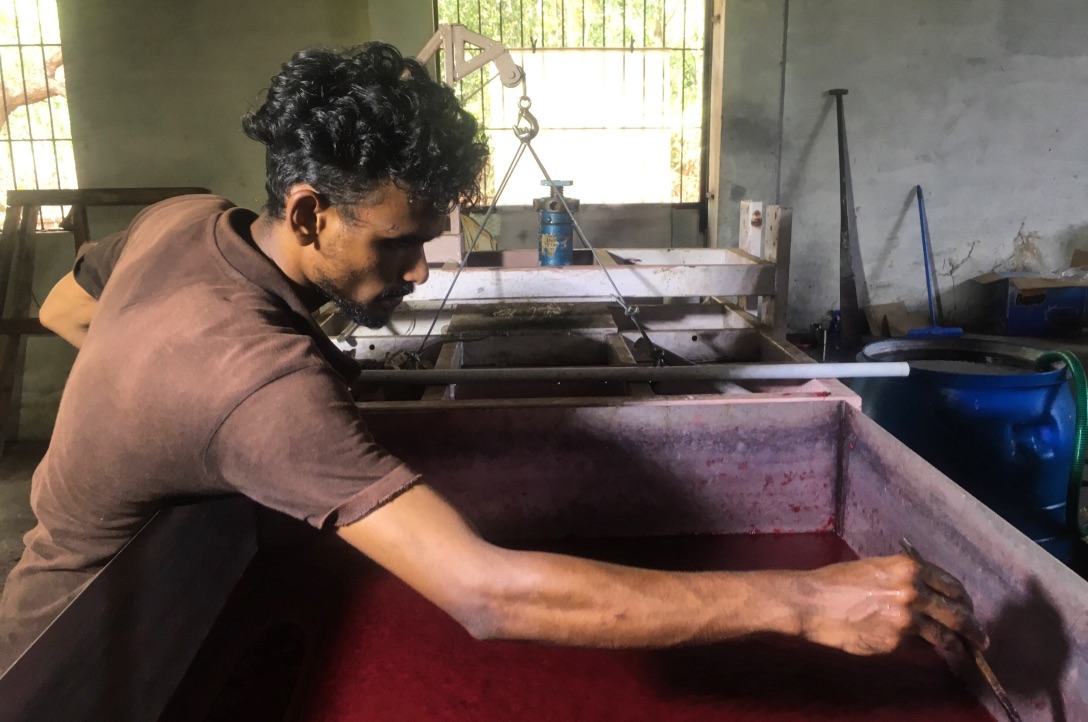
2
Could you describe the progress of work on a specific project? From the basic assignment to how do you hand over work to colleagues?
Over the past two years, the nature of our work has changed a lot due to the pandemic. We couldn't travel and visit labs, so we did a lot of experimental work on our own. The Institute of Technology helps us identify the research strategy, consults with us on secondary research and proposes specific steps for practical research with us. Then we do the practical research, as production is in full swing. We send the results back to the institute, where they are tested and analysed, which we then discuss together. We do this quite often. Initially, it took a while to coordinate some cross-disciplinary vocabulary, as each field has its own terminology and jargon. This interdisciplinary communication and cooperation brings many new views and perspectives, which form a very important part of research. After that, it depends on the specific project, whether they help us introduce a specific result into production, which in turn is the next stage. Some research requires a strict protocol, but some practical research is done directly by us and it's then easier for us to put it straight into production.
Over the past two years, the nature of our work has changed a lot due to the pandemic. We couldn't travel and visit labs, so we did a lot of experimental work on our own. The Institute of Technology helps us identify the research strategy, consults with us on secondary research and proposes specific steps for practical research with us. Then we do the practical research, as production is in full swing. We send the results back to the institute, where they are tested and analysed, which we then discuss together. We do this quite often. Initially, it took a while to coordinate some cross-disciplinary vocabulary, as each field has its own terminology and jargon. This interdisciplinary communication and cooperation brings many new views and perspectives, which form a very important part of research. After that, it depends on the specific project, whether they help us introduce a specific result into production, which in turn is the next stage. Some research requires a strict protocol, but some practical research is done directly by us and it's then easier for us to put it straight into production.
"Interdisciplinary communication and collaboration brings many new perspectives, which is a very important part of research."
In your opinion, is it difficult at first to understand each other during such cooperation with experts from other fields?
Everyone has a different point of view, that's the most rewarding and unique thing about it. Often when we cooperate with one institute, one group of scientists, then we may further consult with other experts and it ends up processed by a wide community of experts, which all express themselves differently. From experience, it's very important to do it in such a broad way, because one can form a much better picture from such a wide range of opinions.
It's quite normal that the research is discussed with different experts, often the scientists themselves lead us to get an opinion from someone else. They themselves realise that the more opinions we have at our disposal, the more objective the conclusion will be. So sometimes we also have joint meetings, sometimes we invite an expert who has practical experience directly from production.
In the academic sphere, designers increasingly work with experts physically in the laboratory. Do you think it's rather an exception in practice? At the very least, it's certainly time-consuming and costly, along with production.
It's certainly difficult to coordinate. The big companies already have their own labs where they can devote themselves to innovations, but their cooperation methodology will be different, and the environment is probably a bit more competitive. As for the smaller companies, few can afford their own lab. If they are companies operating, e.g., in London or New York City, they're already part of some infrastructure where it's possible to rent a small lab. Unfortunately, such facilities don't yet exist in India.
When you mentioned technical institutes, did you mean any specific ones that you cooperate with on a regular basis? Are these Indian or European institutions?
For something that involves hands-on research, it's a good idea to choose places you can physically visit or have them visit you. But as I already mentioned, the scientific community is very open, so when it comes to consultations or research, geographical location doesn't play a role. We select experts according to focus; so according to publications, work experience, etc. Of course, also according to location, so that we can travel to them or send samples, since our research is also practical. In particular, we cooperate with Hyderabad Institute of Technology and Management and Cochin University of Science and Technology.
What roles do you play as a designer in your company?
I play many different roles. Some are closer to me, some not at all, so I hope that over time I'll get rid of some of them. Those roles are difficult to categorise, since they all influence each other. It doesn't work like in a large corporation, where responsibility is precisely distributed. I started with a more scientific method of work, because I was concerned with how exactly bacterial cellulose functions and works. However, I didn't know what professional dictionary to use, how to convert measurements, etc. Over time, I learned these kinds of things just by working with laboratories and professionals. As a designer, I know what I want from the project and what my vision is. So I know what properties of the material to focus on, i.e. what reminds me of leather or textile. I know how to connect the material by sewing and how to create a bag from it, for example. I'm trying to move the material to some stage and see if it works at all. I have to consider the visuals, the communication of how the material will further affect the people who will be dealing with it. As a designer, I always have to maintain a line in which the product will be visually appealing, not just a tasteless substitute for another material.
Furthermore, I have to take into account some design-environmental aspects, i.e. what will happen to the material at the end of the product's life. Whether it can be further used for another product, whether it can be composted, what the composting protocol is, what specific components it breaks down into – that's the scientific side, based on chemistry itself. It's also necessary to understand the process of mechanisation of production, where initially it was more Susmith's expertise; how to mechanise these operations, how to choose the right tool to achieve the required parameters. You have to understand the entire process of design and development of a certain machine, which is very complex and time-consuming. The learning curve was very big and to this day some machines take us years to develop due to their complexity.
And, of course, for the last three years, I've also been dealing with the business role, which I hope to hand over to a business person very soon. It's about the whole economy of the project; who we actually sell to, what makes up the price of the product, how it fits into the business segment we want to get into, where we want to move the project in a few years, how to get there... There are really many roles and I hold several of them, but the one closest to me is definitely the design one, and the design-scientific one, where I apply scientific research methodologies.
Regarding interdisciplinary cooperation, do you think it's an essential part of every design practice? That is, is it possible to develop truly environmentally friendly products even without it?
I think that in every innovation, interdisciplinary communication and cooperation is very important, even crucial. When creating anything new – a product, material, or service – different perspectives must be taken into account. Environmental responsibility has been a topic for the last two decades, but as can be seen in various publications and researches, the scientific community as a whole is beginning to be oriented to offer solutions and better, more responsible options in this regard.
But if such cooperation was natural and at the beginning of innovation projects, the team included experts of different fields, wouldn't the design/development process become more efficient?
Well, inter-professional cooperation is not easy at all. Not everyone can do it. You have to have an open mind and adjust to the fact that you aren't always right and your point of view isn't always relevant. This is contrary to the human ego, so such cooperation isn't always successful. Not everyone is suited to it. Some people will be better off in their field. Interprofessional cooperation is for people who have an open mind, can accept constructive criticism, can process information of a different type than they are used to, and are open to new knowledge and methodologies. I think it's important, but I don't think it's for everyone. It also depends on the specific project, whether it's appropriate or it's just an excuse to extend the project, to answer questions that are really not that important. But it's certainly always beneficial for those innovations.
Everyone has a different point of view, that's the most rewarding and unique thing about it. Often when we cooperate with one institute, one group of scientists, then we may further consult with other experts and it ends up processed by a wide community of experts, which all express themselves differently. From experience, it's very important to do it in such a broad way, because one can form a much better picture from such a wide range of opinions.
It's quite normal that the research is discussed with different experts, often the scientists themselves lead us to get an opinion from someone else. They themselves realise that the more opinions we have at our disposal, the more objective the conclusion will be. So sometimes we also have joint meetings, sometimes we invite an expert who has practical experience directly from production.
In the academic sphere, designers increasingly work with experts physically in the laboratory. Do you think it's rather an exception in practice? At the very least, it's certainly time-consuming and costly, along with production.
It's certainly difficult to coordinate. The big companies already have their own labs where they can devote themselves to innovations, but their cooperation methodology will be different, and the environment is probably a bit more competitive. As for the smaller companies, few can afford their own lab. If they are companies operating, e.g., in London or New York City, they're already part of some infrastructure where it's possible to rent a small lab. Unfortunately, such facilities don't yet exist in India.
When you mentioned technical institutes, did you mean any specific ones that you cooperate with on a regular basis? Are these Indian or European institutions?
For something that involves hands-on research, it's a good idea to choose places you can physically visit or have them visit you. But as I already mentioned, the scientific community is very open, so when it comes to consultations or research, geographical location doesn't play a role. We select experts according to focus; so according to publications, work experience, etc. Of course, also according to location, so that we can travel to them or send samples, since our research is also practical. In particular, we cooperate with Hyderabad Institute of Technology and Management and Cochin University of Science and Technology.
What roles do you play as a designer in your company?
I play many different roles. Some are closer to me, some not at all, so I hope that over time I'll get rid of some of them. Those roles are difficult to categorise, since they all influence each other. It doesn't work like in a large corporation, where responsibility is precisely distributed. I started with a more scientific method of work, because I was concerned with how exactly bacterial cellulose functions and works. However, I didn't know what professional dictionary to use, how to convert measurements, etc. Over time, I learned these kinds of things just by working with laboratories and professionals. As a designer, I know what I want from the project and what my vision is. So I know what properties of the material to focus on, i.e. what reminds me of leather or textile. I know how to connect the material by sewing and how to create a bag from it, for example. I'm trying to move the material to some stage and see if it works at all. I have to consider the visuals, the communication of how the material will further affect the people who will be dealing with it. As a designer, I always have to maintain a line in which the product will be visually appealing, not just a tasteless substitute for another material.
Furthermore, I have to take into account some design-environmental aspects, i.e. what will happen to the material at the end of the product's life. Whether it can be further used for another product, whether it can be composted, what the composting protocol is, what specific components it breaks down into – that's the scientific side, based on chemistry itself. It's also necessary to understand the process of mechanisation of production, where initially it was more Susmith's expertise; how to mechanise these operations, how to choose the right tool to achieve the required parameters. You have to understand the entire process of design and development of a certain machine, which is very complex and time-consuming. The learning curve was very big and to this day some machines take us years to develop due to their complexity.
And, of course, for the last three years, I've also been dealing with the business role, which I hope to hand over to a business person very soon. It's about the whole economy of the project; who we actually sell to, what makes up the price of the product, how it fits into the business segment we want to get into, where we want to move the project in a few years, how to get there... There are really many roles and I hold several of them, but the one closest to me is definitely the design one, and the design-scientific one, where I apply scientific research methodologies.
Regarding interdisciplinary cooperation, do you think it's an essential part of every design practice? That is, is it possible to develop truly environmentally friendly products even without it?
I think that in every innovation, interdisciplinary communication and cooperation is very important, even crucial. When creating anything new – a product, material, or service – different perspectives must be taken into account. Environmental responsibility has been a topic for the last two decades, but as can be seen in various publications and researches, the scientific community as a whole is beginning to be oriented to offer solutions and better, more responsible options in this regard.
But if such cooperation was natural and at the beginning of innovation projects, the team included experts of different fields, wouldn't the design/development process become more efficient?
Well, inter-professional cooperation is not easy at all. Not everyone can do it. You have to have an open mind and adjust to the fact that you aren't always right and your point of view isn't always relevant. This is contrary to the human ego, so such cooperation isn't always successful. Not everyone is suited to it. Some people will be better off in their field. Interprofessional cooperation is for people who have an open mind, can accept constructive criticism, can process information of a different type than they are used to, and are open to new knowledge and methodologies. I think it's important, but I don't think it's for everyone. It also depends on the specific project, whether it's appropriate or it's just an excuse to extend the project, to answer questions that are really not that important. But it's certainly always beneficial for those innovations.
"Interdisciplinary cooperation is for people who have an open mind and can accept constructive criticism, information of a different type than they are used to, and are open to new knowledge and methodologies."
You just mentioned an interesting thing that I wanted to ask you too. Can you think of any tips or tools for those who want to collaborate in this way as a team? What prerequisites or qualities besides an open mind should such people have?
I believe there are experts in interdepartmental communication who would definitely advise you on some specific tools. Vlasta from 'Crafting Plastics' organises such a meeting every year: the Deposium. Last year, there was Maya Shmailov, Ph.D. from a university in Israel, who did a workshop for us. Unfortunately, I don't quite remember the tools, but it's always about communication. You need to connect professionally first, but it's good if your personal aspect is different, e.g. origin, culture. Then the way of communication is also fundamentally different and it's good to get to know each other as human beings, as part of some exercises. Just last year at that workshop, we had an exercise where we presented various topics and talked about how we understood the topics. We often speak the same language, but the interpretation of our words is individual. These are simple exercises that are basically a game, but they can prepare you as a group for the fact that you will not always understand each other, that communication is essential, and it's important to recognise where and what you don't understand. It's important to know that it isn't a matter of differences in knowledge, only in communication terminology, in order to exchange that knowledge effectively.
I believe there are experts in interdepartmental communication who would definitely advise you on some specific tools. Vlasta from 'Crafting Plastics' organises such a meeting every year: the Deposium. Last year, there was Maya Shmailov, Ph.D. from a university in Israel, who did a workshop for us. Unfortunately, I don't quite remember the tools, but it's always about communication. You need to connect professionally first, but it's good if your personal aspect is different, e.g. origin, culture. Then the way of communication is also fundamentally different and it's good to get to know each other as human beings, as part of some exercises. Just last year at that workshop, we had an exercise where we presented various topics and talked about how we understood the topics. We often speak the same language, but the interpretation of our words is individual. These are simple exercises that are basically a game, but they can prepare you as a group for the fact that you will not always understand each other, that communication is essential, and it's important to recognise where and what you don't understand. It's important to know that it isn't a matter of differences in knowledge, only in communication terminology, in order to exchange that knowledge effectively.
"We often speak the same language, but the interpretation of our words is individual, ... it's important to know that it isn't a matter of differences in knowledge, only in communication terminology, in order to exchange that knowledge effectively."
You mentioned that the designer must take into account the communication of the material or product with the public. Do you think that good communication skills are essential for the design profession? I mean communication both externally and within the company.
It depends, I run the company, so in my position I really have to be sure whether people understand me or not. I don't think that it's always the role of the designer, although they often have this bridging role because they communicate between the group of people who make the product and the product's target group. Therefore, designers must understand and be able to communicate with both ends of the spectrum.
It depends, I run the company, so in my position I really have to be sure whether people understand me or not. I don't think that it's always the role of the designer, although they often have this bridging role because they communicate between the group of people who make the product and the product's target group. Therefore, designers must understand and be able to communicate with both ends of the spectrum.

3
Let's move on to your studies. You studied Textile Futures (2012-2014), which was recently renamed Material Futures. It was founded by Carole Collet around the year 2000. Why did you choose this Master's course for your follow-up studies?
I don't even know anymore, it was such a long time ago. :)
I first studied in Liberec, then I went to Istanbul for two years, where I also stayed to work. It's a completely different environment than the Czech Republic, where the design scene is terribly small, whereas in Turkey the industry is huge. The role of the designer is really visible there, you know where you can use your experience and where to get it. There are so many options. I worked there for about 2-3 years while studying. I liked my work, even though I got to really different industrial districts; I saw the conditions in which people live and work there, and the conditions in which things are created. Overall, I felt that the people who work in the underbelly of the industry are terribly underappreciated – financially but also in general – from the outside world of fashion. It didn't seem entirely fair to me. This part of manufacturing is exactly what people don't see and don't know, catwalks are a very distant part of this industry. I also focused on this when looking for a master's degree – on a different perspective within fashion. Back then, there was a department at UAL led by Susan Posthlethwaite, something like 'Sustainable Fashion', but I found it to be too theoretical. Within design, I am more practically oriented. Then I heard about 'Textile Futures'. I found it especially practically oriented and very interesting, even though it was more difficult for me to understand. The hands-on approach appealed to me, so I applied there and went for an interview. At the time, my portfolio was quite focused on fashion, so I convinced them that I also knew other things and they admitted me. At that time, it was based on the work of Carole Collet. Of course, the people in that course kept changing, so we saw Carole herself a few times during the whole time. But it was very interesting.
Based on the interview with Carole Collet (published in Material Times 2), I wanted to ask you, if you can confirm that this field was focused on the integration of designers and scientists already within the studies. Do I understand correctly that this was her intention at the time of founding? Do you think the field has fulfilled this purpose?
Yes, definitely. At first it was very confusing, I remember we were bombarded with various short-term projects in the first year. For example, every Wednesday they brought us someone for a talk/presentation and these people weren't just designers, they were various experts: a doctor who worked somewhere in Antarctica, a scientist from NASA, etc. Sometimes I didn't even understand where they got them from. It was very beneficial though. We also had workshops focused on cooperation with students from other fields within the school. And it was already obvious that cooperation could sometimes be very difficult, not everyone was used to a different dynamic. For example, many designers were used to handing out roles and responsibilities to others, and that's not really what it's about. That first year was pretty confusing anyway. The second year was already focused on our final project, and we were already looking for our own experts and managing the entire project. Also, our mentors didn't always have enough experience with the given subject/topic that we chose ourselves. So I guess Carole Collet got it right, at least I think.
Did you have a lab at your school where you could work as part of the local interdisciplinary cooperation? Or what did the shared spaces for work look like at school?
There weren't any laboratories at that time, but I think there will be some by now, since they also have a branch focused on it, which is very nice. We had to look for labs ourselves or somehow create them. We had access to workshops, they were quite nice, but they were more for processing wood, metal, plastics, for making prototypes. There was also a workshop focused on AI, but otherwise nothing from other fields.
Can you estimate how many of you were in the year?
About 10.
And most of the students were focused on textiles?
I think so, but we had people from architecture, multimedia, a lady with a science degree, and various design branches.
The lady scientist was directly with you in the year?
Actually, there were two of them, and apart from the fact that they were from a completely different field, they were both over sixty years old. So they brought a completely different dynamic and perspective to those discussions.
The field is created by the students themselves, the people you meet there. Did you often consult your projects with classmates?
We had some sessions every Wednesday, in the literal translation something like 'critical sessions', where we had to arrive in the morning, everyone had to present their project and everyone commented on it. Regarding a specific issue, they gave us their perspective or suggested what we should focus on. When we were dealing with a problem, we could discuss it together. That was very nice and it also brought us together as a team, brought us closer as people, and we learned a lot about presenting, since we practised it every week.
When you compare it with Czech education, did you miss this dialogue?
It was quite different; on one hand, the studies, on the other hand, we were several years younger. But the dynamics was different in Czechia. We definitely talked in the collective as well, but only after the mentors left. They somehow didn't ask, they told us their opinion and then we discussed it ourselves. But you certainly didn't have the same feeling as in London, where we actually got to be equals. Where your opinion of a colleague was not irrelevant, it had its own weight.
It seems to me that in the Czech environment, this dialogic way of (not only) design education is, unfortunately, still not a matter of course. My experience with 'Furniture Design' (Mendel University) was also similar; none of the teachers were interested in our opinion. Only at FaVU (BUT) did I encounter this open and more collective approach. But things are slowly changing for the better.
I hope so, although the bachelor's degree often has a different dynamic than the master's degree.
In the second year, the study (or work on the diploma project) was under your direction. Were the teachers available to you, did they help you establish contacts when needed?
It depended on what one chose. If they could help us or knew someone who could, then certainly yes. However, when they didn't know anyone (or the topic), they were probably in the same starting position as us. In my case they didn't know anyone in particular. There was only one person who had worked with bacterial cellulose before, and that was Susan Lee. So they sent me to her, I interviewed her and it was again a perspective from which to look at it, just very similar to mine. Then I found other experts directly from the scientific community, which was much more informative for me, because I gained knowledge from a different point of view.
At what stage of the project development did you contact the scientists? To what extent did you research the material?
At the beginning, I didn't have any specific idea. I just knew that I wanted to map various bio-organisms that could have an interesting role within this technology; when they create something, transform it, or simply function as catalysts. That's when I found Dr. Simon Park from the University of Surrey, he had a blog at the time, bioart was the hype, so I contacted him. He was such a strange gentleman, but he basically gave me an intro to basic microbiology methodologies. He showed me the lab, how to clone a culture, what it looks like in an incubator. I then designed a few experiments that he set up in that laboratory. Along with that, I found an expert from Chile who is a microbiologist. She deals with conservation, so she gave me a different point of view on it and advised me on the literature to study.
Then I worked my way up to bacterial cellulose itself; like with many other microorganisms, not everything worked out for me experimentally, or I didn't have access to some processing that was needed. It was quite an organic development. Because I was also dealing with technical problems, I found many experts from the publications in which they participated. Later, while assembling the whole machine, I connected with engineers from HackSpace. So in my case it was a huge number of people I communicated with.
It would've been easier if I'd known from the beginning what I wanted to do, but that wasn't the case. I'd recommend this approach to people who are going for a master's degree – it will save them a lot of time. But if you don't know exactly what you want to do, like me, it's actually very educational. I slowly cut down the things I didn't want in the project, step by step, until finally I was left with the ones I wanted to focus on. But I had to carve it from a very large mass.
That's great that you made it. From my experience and from other conversations, I've found out that if you speak too generally, you will not meet with much success with scientists.
Yes, that's right. You have to ask them more direct questions, because they are used to a completely different style of work. They're used to solving specific problems. So I really read a lot in the beginning, I went through a lot of information in order to first understand it from the secondary research and only then I contacted people with more direct questions. Many people didn't answer, many did... And you also learn to ask the question correctly, because no one will answer questions that lead nowhere, since these people usually have a lot to do. So yes, I did a lot of theoretical research by myself for a long time, the first 5 months for sure.
I don't even know anymore, it was such a long time ago. :)
I first studied in Liberec, then I went to Istanbul for two years, where I also stayed to work. It's a completely different environment than the Czech Republic, where the design scene is terribly small, whereas in Turkey the industry is huge. The role of the designer is really visible there, you know where you can use your experience and where to get it. There are so many options. I worked there for about 2-3 years while studying. I liked my work, even though I got to really different industrial districts; I saw the conditions in which people live and work there, and the conditions in which things are created. Overall, I felt that the people who work in the underbelly of the industry are terribly underappreciated – financially but also in general – from the outside world of fashion. It didn't seem entirely fair to me. This part of manufacturing is exactly what people don't see and don't know, catwalks are a very distant part of this industry. I also focused on this when looking for a master's degree – on a different perspective within fashion. Back then, there was a department at UAL led by Susan Posthlethwaite, something like 'Sustainable Fashion', but I found it to be too theoretical. Within design, I am more practically oriented. Then I heard about 'Textile Futures'. I found it especially practically oriented and very interesting, even though it was more difficult for me to understand. The hands-on approach appealed to me, so I applied there and went for an interview. At the time, my portfolio was quite focused on fashion, so I convinced them that I also knew other things and they admitted me. At that time, it was based on the work of Carole Collet. Of course, the people in that course kept changing, so we saw Carole herself a few times during the whole time. But it was very interesting.
Based on the interview with Carole Collet (published in Material Times 2), I wanted to ask you, if you can confirm that this field was focused on the integration of designers and scientists already within the studies. Do I understand correctly that this was her intention at the time of founding? Do you think the field has fulfilled this purpose?
Yes, definitely. At first it was very confusing, I remember we were bombarded with various short-term projects in the first year. For example, every Wednesday they brought us someone for a talk/presentation and these people weren't just designers, they were various experts: a doctor who worked somewhere in Antarctica, a scientist from NASA, etc. Sometimes I didn't even understand where they got them from. It was very beneficial though. We also had workshops focused on cooperation with students from other fields within the school. And it was already obvious that cooperation could sometimes be very difficult, not everyone was used to a different dynamic. For example, many designers were used to handing out roles and responsibilities to others, and that's not really what it's about. That first year was pretty confusing anyway. The second year was already focused on our final project, and we were already looking for our own experts and managing the entire project. Also, our mentors didn't always have enough experience with the given subject/topic that we chose ourselves. So I guess Carole Collet got it right, at least I think.
Did you have a lab at your school where you could work as part of the local interdisciplinary cooperation? Or what did the shared spaces for work look like at school?
There weren't any laboratories at that time, but I think there will be some by now, since they also have a branch focused on it, which is very nice. We had to look for labs ourselves or somehow create them. We had access to workshops, they were quite nice, but they were more for processing wood, metal, plastics, for making prototypes. There was also a workshop focused on AI, but otherwise nothing from other fields.
Can you estimate how many of you were in the year?
About 10.
And most of the students were focused on textiles?
I think so, but we had people from architecture, multimedia, a lady with a science degree, and various design branches.
The lady scientist was directly with you in the year?
Actually, there were two of them, and apart from the fact that they were from a completely different field, they were both over sixty years old. So they brought a completely different dynamic and perspective to those discussions.
The field is created by the students themselves, the people you meet there. Did you often consult your projects with classmates?
We had some sessions every Wednesday, in the literal translation something like 'critical sessions', where we had to arrive in the morning, everyone had to present their project and everyone commented on it. Regarding a specific issue, they gave us their perspective or suggested what we should focus on. When we were dealing with a problem, we could discuss it together. That was very nice and it also brought us together as a team, brought us closer as people, and we learned a lot about presenting, since we practised it every week.
When you compare it with Czech education, did you miss this dialogue?
It was quite different; on one hand, the studies, on the other hand, we were several years younger. But the dynamics was different in Czechia. We definitely talked in the collective as well, but only after the mentors left. They somehow didn't ask, they told us their opinion and then we discussed it ourselves. But you certainly didn't have the same feeling as in London, where we actually got to be equals. Where your opinion of a colleague was not irrelevant, it had its own weight.
It seems to me that in the Czech environment, this dialogic way of (not only) design education is, unfortunately, still not a matter of course. My experience with 'Furniture Design' (Mendel University) was also similar; none of the teachers were interested in our opinion. Only at FaVU (BUT) did I encounter this open and more collective approach. But things are slowly changing for the better.
I hope so, although the bachelor's degree often has a different dynamic than the master's degree.
In the second year, the study (or work on the diploma project) was under your direction. Were the teachers available to you, did they help you establish contacts when needed?
It depended on what one chose. If they could help us or knew someone who could, then certainly yes. However, when they didn't know anyone (or the topic), they were probably in the same starting position as us. In my case they didn't know anyone in particular. There was only one person who had worked with bacterial cellulose before, and that was Susan Lee. So they sent me to her, I interviewed her and it was again a perspective from which to look at it, just very similar to mine. Then I found other experts directly from the scientific community, which was much more informative for me, because I gained knowledge from a different point of view.
At what stage of the project development did you contact the scientists? To what extent did you research the material?
At the beginning, I didn't have any specific idea. I just knew that I wanted to map various bio-organisms that could have an interesting role within this technology; when they create something, transform it, or simply function as catalysts. That's when I found Dr. Simon Park from the University of Surrey, he had a blog at the time, bioart was the hype, so I contacted him. He was such a strange gentleman, but he basically gave me an intro to basic microbiology methodologies. He showed me the lab, how to clone a culture, what it looks like in an incubator. I then designed a few experiments that he set up in that laboratory. Along with that, I found an expert from Chile who is a microbiologist. She deals with conservation, so she gave me a different point of view on it and advised me on the literature to study.
Then I worked my way up to bacterial cellulose itself; like with many other microorganisms, not everything worked out for me experimentally, or I didn't have access to some processing that was needed. It was quite an organic development. Because I was also dealing with technical problems, I found many experts from the publications in which they participated. Later, while assembling the whole machine, I connected with engineers from HackSpace. So in my case it was a huge number of people I communicated with.
It would've been easier if I'd known from the beginning what I wanted to do, but that wasn't the case. I'd recommend this approach to people who are going for a master's degree – it will save them a lot of time. But if you don't know exactly what you want to do, like me, it's actually very educational. I slowly cut down the things I didn't want in the project, step by step, until finally I was left with the ones I wanted to focus on. But I had to carve it from a very large mass.
That's great that you made it. From my experience and from other conversations, I've found out that if you speak too generally, you will not meet with much success with scientists.
Yes, that's right. You have to ask them more direct questions, because they are used to a completely different style of work. They're used to solving specific problems. So I really read a lot in the beginning, I went through a lot of information in order to first understand it from the secondary research and only then I contacted people with more direct questions. Many people didn't answer, many did... And you also learn to ask the question correctly, because no one will answer questions that lead nowhere, since these people usually have a lot to do. So yes, I did a lot of theoretical research by myself for a long time, the first 5 months for sure.
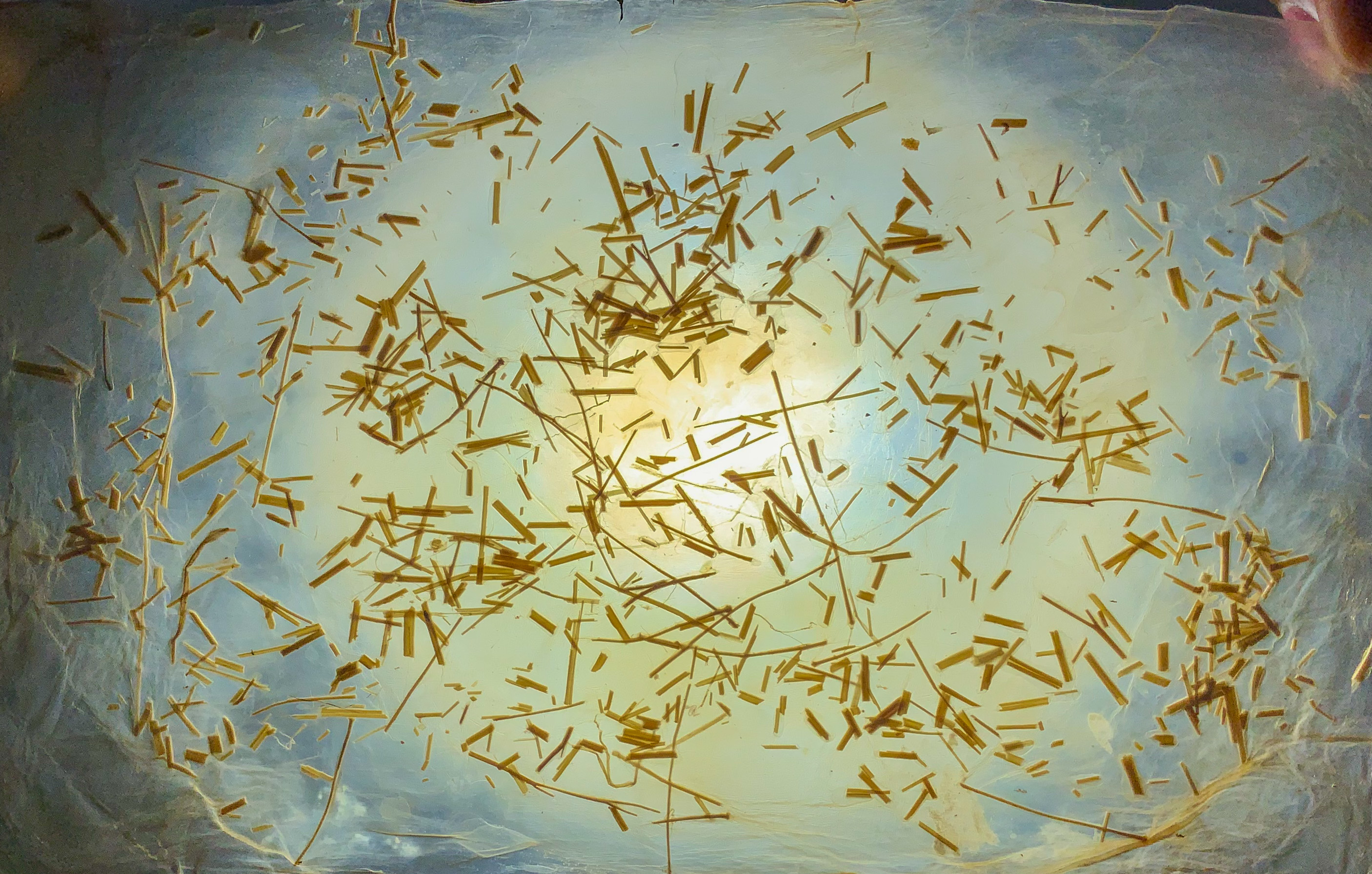
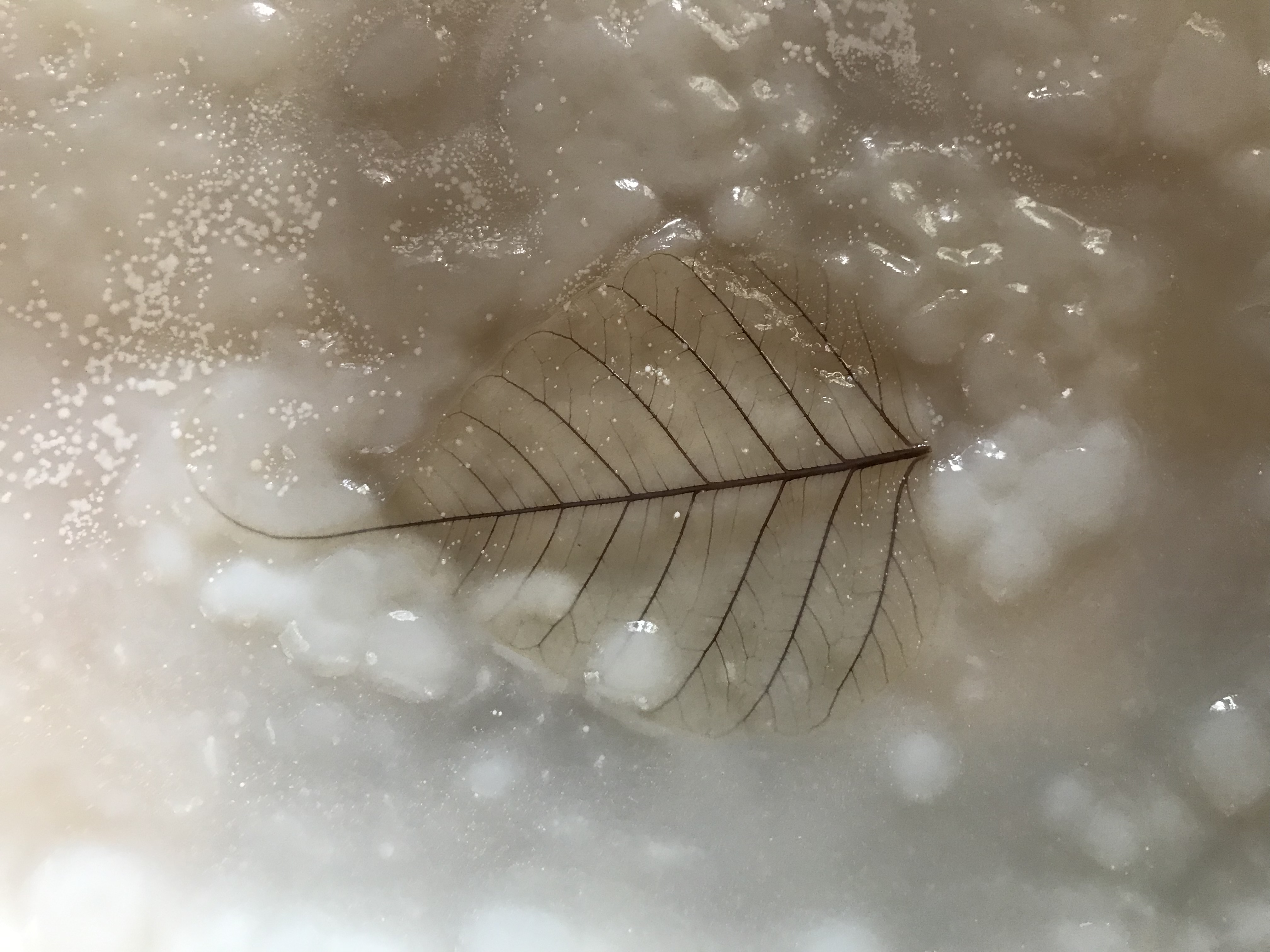
4
Currently (October 2023), the project ZRAST-LINY n which you worked on last year together with Vladimíra Maťašejová, the author of the Story of Linen project, is exhibited in the library of the Bratislava Goethe-Institut (the project is mentioned on the website in the Approaches section ︎︎︎ Tradition and local approach.) Can you please describe how the research was conducted and summarise your conclusions and outputs? As the name and your specialisation suggest, this is probably the development of biocomposites connecting local, Slovak plant resources (flax, hemp, linden, etc.) with bacterial cellulose.
I connected with Vladimíra because she works with the local production of flax in Slovakia and grows it herself. This was interesting for me, because for a few years I have been studying and experimenting with plant fibres growing in Slovakia (flax, hemp, nettle, clover, corn, linen...).
Especially at the beginning, our cooperation often developed in the form of conversations about what we do, what experiments we'd like to carry out and what dimension it would give to our practice.
We identified flax fibres that Vladimíra doesn't further process into woven textiles and decided to use these for the experiments. Then followed the design of the experiment from my side – using the technique of overgrowth and vertical growth of bacterial cellulose. We investigated how fibres cooperate with bacterial cellulose (if at all), what structures they create together, whether the given structures are interesting in terms of their appearance or their properties.
The outputs were, on one hand, material samples of these so-called growths and, on the other hand, production process protocols, which were designed and used during the experiments.
Interviewed by Valentýna Landa Filípková
1 Foto: Petr Fabo, Zuzana with her material
2 Foto: Petr Fabo, photo from the production process of Malai material
3 Foto: Maial.eco, samples of Malai Biomaterials products
4 Foto: archiv Zuzany, photo documentation of the project and exhibition ZRAST-LINY
2 Foto: Petr Fabo, photo from the production process of Malai material
3 Foto: Maial.eco, samples of Malai Biomaterials products
4 Foto: archiv Zuzany, photo documentation of the project and exhibition ZRAST-LINY