22. 4. 2021 Material design
Paula Nerlich
Paula Nerlich
Paula Nerlich
is a material designer and a co-founder of a virtual workshop series called Circular Home Lab. Participants of the series are introduced with a circular economy concept and are taught how to use their own food waste to create materials and products. Paula is also a postgraduate student of Biodesign at Newcastle University and a researcher at HBBE.
is a material designer and a co-founder of a virtual workshop series called Circular Home Lab. Participants of the series are introduced with a circular economy concept and are taught how to use their own food waste to create materials and products. Paula is also a postgraduate student of Biodesign at Newcastle University and a researcher at HBBE.

1
I am interested in the general topic of changing the role of a designer from designing things to contributing to the community; especially by creating and sharing knowledge and experience for the better future. I suppose that is exactly what your project Circular Home Lab (or for example platform Materiom with open-source recipes) does. The project Circular Home Lab mediates online workshops for various communities and companies, in which participants create materials and products from their food waste. These workshops also connect people from all over the world. Could you describe how the workshops work? How and when did you come up with this idea? Has the pandemic, in some way, influenced this initiative?
Paula: I met with the co-founder of Circular Home Lab, Vanessa Rosenthal, one and a half years ago at the exhibition ‘Biodesign Here Now’, where I was showing my material work. When Vanessa visited my stand, we started talking and, basically, our conversation continues to this day. Both of us come from very different backgrounds - me from Material Design and Vanessa from Business Design. 2 With Circular Home Lab, we bring together our perspectives to reflect upon current systems and new material narratives around waste.
We founded the virtual workshop series during the pandemic to reach out to people while also connecting them globally. As the pandemic is still ongoing, we see great value in building up this global network of curious minds, who raise awareness around waste and new economic systems that can drive more sustainable future.
Within the workshops, we start off with what we call ‘Systems Complexity’ where we dive into the current and future economic systems, especially around food waste. We further look at biomaterials and interesting cases (material Start-Ups …) to paint a picture of what is currently out there and what future narratives could be told. After that, we have a fun material making session where the participants and I create an object from our household food waste (surplus) to, as we like to say, ‘turn the new thoughts into tangible matter’. This is a wonderful experiential way of continuing the discourse around matters introduced in the first part of the workshop.
In Circular Home Lab workshops, people make objects from scratch. Can this consumer/customer participation in production process create a bigger emotional connection between people and the products? Do you think it can be a path for better future in terms of reducing waste in general?
Paula: This deeper connection is exactly what we aim for. If we can understand the story behind an object, its origin, the making process, and how we can take care of it better, we will automatically treat it in a different way. Hopefully, it will be in more conscious and sustainable ways. This is for sure nourishing more sustainable pathways and has a potential to reduce waste through consumer behaviour as well as new product design.
I admire your work and I am also interested in recreating food waste into materials, especially when they are used as packaging for other food products. For example, I tried to create a material from brewer's grain. This is an interesting example of using these grains as can holders – Trebodur. Also, I found out that some companies create crackers from these grains, and this makes much more sense to me. Despite all this, I think the world is running towards a food crisis. Food waste and wasting in general is a big topic for discussion. Wouldn’t it be more beneficial to process the food waste into another food?
Paula: Yes, it is crucial to look at all the aspects. If a resource can be used as food for humans, it is considered to be more valuable (ethically as well) than if something else is created from it. Some leftovers are used as food for stock, which is related to the meat or milk/cheese industry. Here I question whether these industries should be supported and whether it is at all healthy for the animals to be fed random food waste that is not their natural choice. Even if we do not have all the information needed, nor all the answers, it is legitimate to question these things and also to make it transparent in your material making process.
You developed two materials made from food waste: Aqua Faba Foam (from chickpeas) and Cocoa (made from chocolate industrial waste). Did you create these materials on your own or did you co-operate with specialists from other fields such as scientists, etc.? Could you describe the material making process? Do you have any tips and tricks for students who want to start making innovative materials without fading into oblivion in their local contexts, and push their way to the market?
Paula: I created both the materials by myself. To get materials ready for market, one still needs to collaborate with material/production/engineering experts of some sort in most cases, which can be tricky to arrange. It takes time, patience, and networking to drive your materials forward. I am afraid I cannot disclose information about the development of my materials, but I can recommend starting collaborations very early on to see which markets would allow super early-stage materials and which need really advanced development. For example, so called Design Objects could be examples of early-stage materials. On the other hand, when you want to launch a product, such as food packaging, it takes development with specialists, such as engineers and packaging experts. In this particular case, you would also need investment. I recommend choosing your collaborations accordingly. Whilst still at university, it is often easy to find someone from a more science or engineering-based course that might be interested in co-founding. Look at NotPLA, who came from university, or Loliware, which was developed by former students who started in their own kitchen and now have big production possibilities.
So, do you want to take the industrial design route, design objects, art or StartUps? Or continue your research at university and do a PhD, where you can again use the fantastic network and knowledge of the uni and some create spin out companies from universities. Such as Orange Fiber from Milan.
Paula: I met with the co-founder of Circular Home Lab, Vanessa Rosenthal, one and a half years ago at the exhibition ‘Biodesign Here Now’, where I was showing my material work. When Vanessa visited my stand, we started talking and, basically, our conversation continues to this day. Both of us come from very different backgrounds - me from Material Design and Vanessa from Business Design. 2 With Circular Home Lab, we bring together our perspectives to reflect upon current systems and new material narratives around waste.
We founded the virtual workshop series during the pandemic to reach out to people while also connecting them globally. As the pandemic is still ongoing, we see great value in building up this global network of curious minds, who raise awareness around waste and new economic systems that can drive more sustainable future.
Within the workshops, we start off with what we call ‘Systems Complexity’ where we dive into the current and future economic systems, especially around food waste. We further look at biomaterials and interesting cases (material Start-Ups …) to paint a picture of what is currently out there and what future narratives could be told. After that, we have a fun material making session where the participants and I create an object from our household food waste (surplus) to, as we like to say, ‘turn the new thoughts into tangible matter’. This is a wonderful experiential way of continuing the discourse around matters introduced in the first part of the workshop.
In Circular Home Lab workshops, people make objects from scratch. Can this consumer/customer participation in production process create a bigger emotional connection between people and the products? Do you think it can be a path for better future in terms of reducing waste in general?
Paula: This deeper connection is exactly what we aim for. If we can understand the story behind an object, its origin, the making process, and how we can take care of it better, we will automatically treat it in a different way. Hopefully, it will be in more conscious and sustainable ways. This is for sure nourishing more sustainable pathways and has a potential to reduce waste through consumer behaviour as well as new product design.
I admire your work and I am also interested in recreating food waste into materials, especially when they are used as packaging for other food products. For example, I tried to create a material from brewer's grain. This is an interesting example of using these grains as can holders – Trebodur. Also, I found out that some companies create crackers from these grains, and this makes much more sense to me. Despite all this, I think the world is running towards a food crisis. Food waste and wasting in general is a big topic for discussion. Wouldn’t it be more beneficial to process the food waste into another food?
Paula: Yes, it is crucial to look at all the aspects. If a resource can be used as food for humans, it is considered to be more valuable (ethically as well) than if something else is created from it. Some leftovers are used as food for stock, which is related to the meat or milk/cheese industry. Here I question whether these industries should be supported and whether it is at all healthy for the animals to be fed random food waste that is not their natural choice. Even if we do not have all the information needed, nor all the answers, it is legitimate to question these things and also to make it transparent in your material making process.
You developed two materials made from food waste: Aqua Faba Foam (from chickpeas) and Cocoa (made from chocolate industrial waste). Did you create these materials on your own or did you co-operate with specialists from other fields such as scientists, etc.? Could you describe the material making process? Do you have any tips and tricks for students who want to start making innovative materials without fading into oblivion in their local contexts, and push their way to the market?
Paula: I created both the materials by myself. To get materials ready for market, one still needs to collaborate with material/production/engineering experts of some sort in most cases, which can be tricky to arrange. It takes time, patience, and networking to drive your materials forward. I am afraid I cannot disclose information about the development of my materials, but I can recommend starting collaborations very early on to see which markets would allow super early-stage materials and which need really advanced development. For example, so called Design Objects could be examples of early-stage materials. On the other hand, when you want to launch a product, such as food packaging, it takes development with specialists, such as engineers and packaging experts. In this particular case, you would also need investment. I recommend choosing your collaborations accordingly. Whilst still at university, it is often easy to find someone from a more science or engineering-based course that might be interested in co-founding. Look at NotPLA, who came from university, or Loliware, which was developed by former students who started in their own kitchen and now have big production possibilities.
So, do you want to take the industrial design route, design objects, art or StartUps? Or continue your research at university and do a PhD, where you can again use the fantastic network and knowledge of the uni and some create spin out companies from universities. Such as Orange Fiber from Milan.
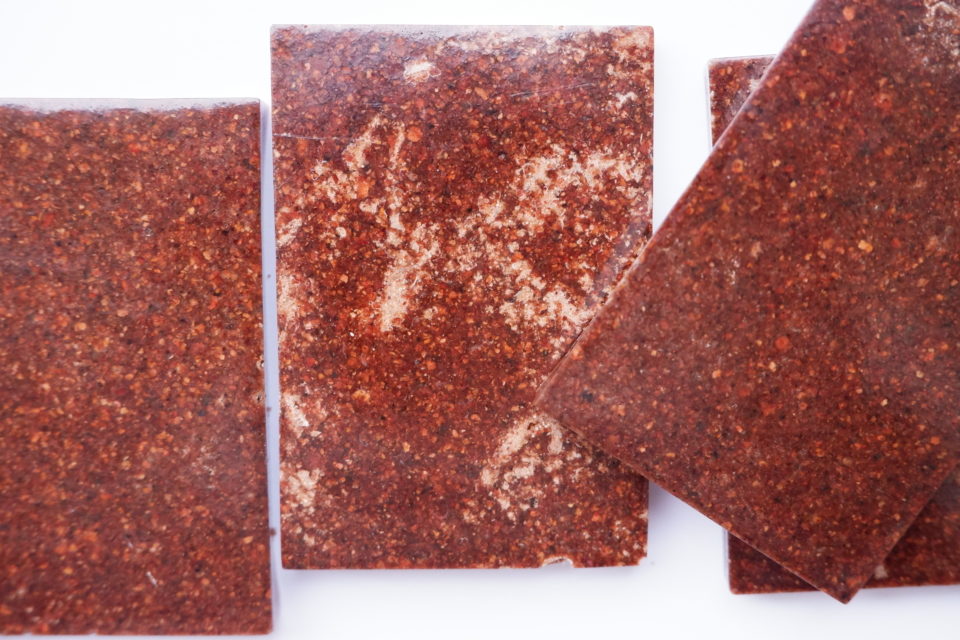
3
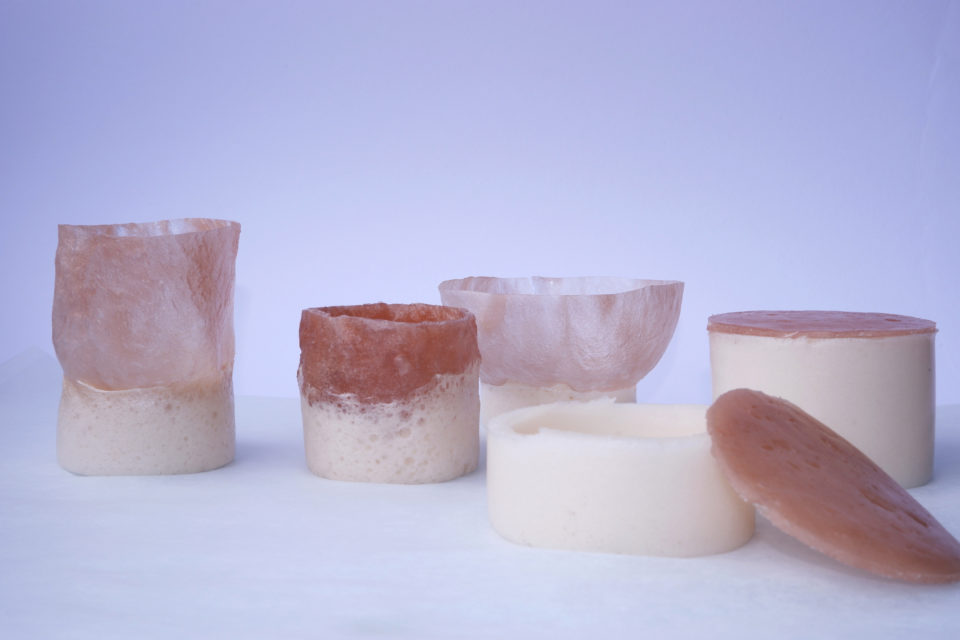
4
1 Paula Nerlich, photo credit: Marielle Samstad
2 Business design incorporates design thinking and similar approaches that put the customer at the center of the design process, but business design goes further by focusing on profitable business models.
3 Cocoa material, photo credit: Material District
4 AquaFaba Foam, photo credit: Material District
2 Business design incorporates design thinking and similar approaches that put the customer at the center of the design process, but business design goes further by focusing on profitable business models.
3 Cocoa material, photo credit: Material District
4 AquaFaba Foam, photo credit: Material District